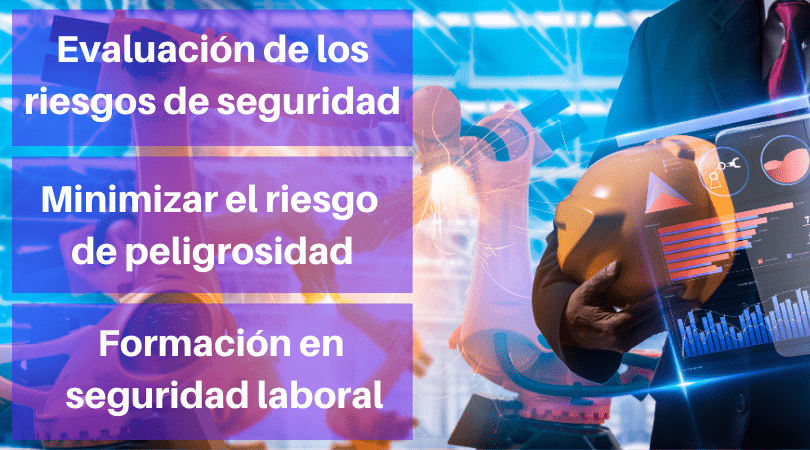
La seguridad en la robótica industrial es primordial. Los fabricantes tienen la responsabilidad de proteger a los trabajadores de lesiones o daños, e incluso han de garantizar el cumplimiento de las normas y el aumento de la productividad en el proceso de mejora de la seguridad.
Para ello deben establecerse mecanismos de seguridad para asegurar que los operarios humanos puedan anular los comportamientos no deseados de los robots de una manera segura.
La instalación de robots industriales requiere medidas de seguridad, un ejercicio costoso y que consume mucho tiempo. Los robots de colaboración pueden ofrecer una solución; sin embargo, estos sistemas sólo cumplen las normas de seguridad si operan a velocidades reducidas.
¿Cuáles son los riesgos potenciales cuando se trabaja con robots industriales?
Existen varios tipos de accidentes que pueden ocurrir cuando se trabaja con robots industriales. Éstos incluyen:
- Accidentes por impacto o colisión resultantes de movimientos impredecibles, mal funcionamiento de componentes o cambios de programa impredecibles, relacionados con el brazo o el equipo periférico del robot.
- Accidentes por aplastamiento y atrapamiento de las extremidades de los trabajadores u otras partes del cuerpo enganchadas entre el brazo de un robot y otros equipos periféricos, o que el trabajador pueda ser físicamente conducido y aplastado por otros equipos periféricos.
- Los accidentes de las piezas mecánicas que resultan de la avería de los componentes para el accionamiento del robot, las herramientas o el efector final, el equipo periférico o su fuente de energía. Entre ellos se incluyen, por ejemplo, el desplazamiento de piezas, el fallo de un mecanismo de agarre o el fallo de las herramientas eléctricas del efector final (por ejemplo, discos de amolar, discos pulidores, herramientas de rebabado, destornilladores eléctricos y destornilladores de tuercas).
- También, pueden producirse accidentes por fugas en líneas de alta presión, destellos de arco, salpicaduras de metal, polvo, interferencias electromagnéticas o de radiofrecuencia.
La identificación del peligro en los sistemas robóticos industriales puede ser uno de los pasos más importantes en la evaluación de los riesgos para la seguridad. Los peligros pueden venir en forma mecánica, eléctrica, térmica, de ruido, de vibración, de radiación, de material o ergonómica.
¿Por qué ocurren los accidentes en la robótica industrial?
Dado el importante riesgo de que se produzcan accidentes, es esencial comprender por qué se producen estos incidentes. En definitiva, estos problemas suelen provenir de errores humanos, errores de control, accesos no autorizados, fallos mecánicos, fuentes ambientales, sistemas de energía e instalaciones inadecuadas.
Con diferencia, la causa más común es el error humano. Los trabajadores se sienten seguros con el equipo y se adaptan a los peligros trabajando en áreas inseguras cuando programan o realizan el mantenimiento de un robot.
Por otra parte, el problema puede venir de un error de programación introducido por el hombre o un error en la conexión de los equipos. Otros peligros pueden ser el resultado de una instalación incorrecta, la falta de un mantenimiento adecuado del equipo y el mal funcionamiento de los sistemas hidráulicos y eléctrico.
Los robots industriales son capaces de realizar potentes movimientos en una gran área, incluso más allá de la base de la unidad. Los cambios en los materiales o en el entorno pueden afectar a los movimientos programados del robot.
El uso de barreras físicas suele proteger a los trabajadores de los peligros de los robots industriales. Sin embargo, los accidentes ocurren.
3 Tips para prevenir los riesgos y mejorar la seguridad en la robótica industrial.
La identificación de las causas de los peligros en la robótica industrial es un paso fundamental y no siempre es una consideración sencilla. Una vez que se identifican los peligros y se establecen las situaciones de interacción robótica, la evaluación de los riesgos de seguridad se simplifica.
El tipo de peligro que se presenta depende de su aplicación, y es igual de dependiente que cuando se interactúa con los robots industriales, como durante su integración, así como en su aprendizaje y en el mantenimiento o la producción de rutina.
Las circunstancias de la interacción, junto con los tipos de peligros, deben evaluarse en relación con los tipos de protocolos de seguridad en la robótica industrial establecidos para evitar lesiones o daños a los trabajadores. Veamos 3 consejos que nos pueden servir para trabajar seguros con robots industriales:
1. Evaluación de los riesgos de seguridad en la robótica industrial
Una evaluación de riesgos es el primer paso fundamental en la seguridad de la robótica industrial que deben realizar las empresas para proteger a los empleados.
Los empresarios industriales deben asegurarse de que los trabajadores entiendan y reconozcan estos peligros de trabajar con robots. Para empezar, incluso antes de que la empresa utilice cualquier robot, es esencial realizar una evaluación de riesgos durante la fase de diseño del mismo.
En este punto, se deben identificar las limitaciones físicas y operacionales del robot industrial, su propósito y su uso (o mal uso). A continuación, se debe señalar cualquier peligro razonablemente previsible y las condiciones peligrosas de seguridad que puedan surgir.
Una consideración importante es la interacción humana durante el ciclo de vida de la máquina y los posibles estados de la misma.
El objetivo es eliminar tantos peligros identificados como sea posible. Luego, a través del proceso de evaluación de riesgos, determinar el tipo apropiado de controles de seguridad funcional a implementar en la robótica industrial para reducir el riesgo a un nivel aceptable.
2. Minimizar el riesgo de peligrosidad en la robótica industrial
La información reunida durante la evaluación de los riesgos determina el tipo de equipo y los controles utilizados para el sistema de control de la seguridad.
Los controles de ingeniería se utilizan para restringir el acceso a una zona de peligro. Pueden incluir el control de cierres de puertas electromecánicos fiables, barreras fijas, sistemas de control de accionamiento a dos manos y dispositivos de detección de presencia como cortinas de luz, escáneres de láser en una área o alfombras de presión, etc.
Estos dispositivos reducen la probabilidad de exposición al peligro (es decir, al daño) pero no reducen la gravedad potencial de la lesión. Los controles industriales suelen ser las medidas preventivas de seguridad menos favorecidas en la robótica industrial, porque siguen dependiendo del ser humano y sólo tienen la posibilidad de reducir la probabilidad de daño.
Estos controles incluyen dispositivos de concienciación, como señales, alarmas sonoras y luces de advertencia visuales para alertar a los trabajadores del peligro. También incluyen procedimientos (funcionamiento y mantenimiento) y capacitación.
3. Formación en la seguridad y prevención de riesgos laborales en la robótica industrial
Es vital para los trabajadores que programan, trabajan, mantienen o reparan robots industriales, recibir una formación técnica adecuada en materia de seguridad para el conocimiento del riesgo inherente a la actividad. En consecuencia, deben poder demostrar su competencia para realizar sus trabajos con seguridad.
Los empresarios deben proporcionan a sus trabajadores equipos de protección individual (EPI) y garantizar que sus empleados utilicen las protecciones adecuadamente. Una buena formación en este campo puede ayudar a minimizar daños en un accidente. Los EPI incluyen protecciones como respiradores, guantes, protectores faciales, protección auditiva, cascos y gafas de seguridad que los trabajadores deben usar como última capa de defensa contra las lesiones. Por lo que deben conocer cómo funcionan y cómo se utilizan.
Conclusiones
Los rápidos avances de la tecnología han introducido muchos tipos de sistemas robóticos físicos en el centro de trabajo.
Los robots industriales ahora pintan, sueldan, empujan, tiran, levantan y ensamblan productos, mientras que los robots de colaboración o colaborativos, al tener uno o más brazos mecánicos, proporcionan a los trabajadores un par de manos extra. También, ayudan a los médicos a realizar tareas quirúrgicas complejas.
Evaluar los riesgos de la robótica industrial es el primer paso para lograr la seguridad robótica en una fábrica. Por consiguiente, una evaluación adecuada de los riesgos de trabajar con robots industriales suele incluir dos pasos: un análisis y una evaluación de riesgos.
Un análisis de riesgos puede ser el proceso más complicado de los dos y a menudo requiere tres pasos diferentes: determinar los límites de la maquinaria robótica, identificar los posibles peligros de seguridad que conlleva la producción y estimar el riesgo de los peligros identificados en el trabajo con la robótica industrial.